Mastering CNC Milling: How Precision
Manufacturing Elevates Craftsmanship
Precision manufacturing plays a crucial role across diverse industries by ensuring consistent quality and meeting stringent specifications. Computer numerical control (CNC) milling is an essential manufacturing technique that enhances efficiency and accuracy in the production process. It utilizes computer-controlled machinery, enabling the creation of complex parts with high precision.
At Unity Precision Manufacturing, we offer state-of-the-art CNC services tailored to meet the exact needs of our clients! Our skilled team uses advanced machinery and cutting-edge software to deliver precision parts with unparalleled accuracy and consistency. We also prioritize customer satisfaction by guaranteeing timely delivery and cost-effectiveness without compromising quality.
How CNC Milling Works
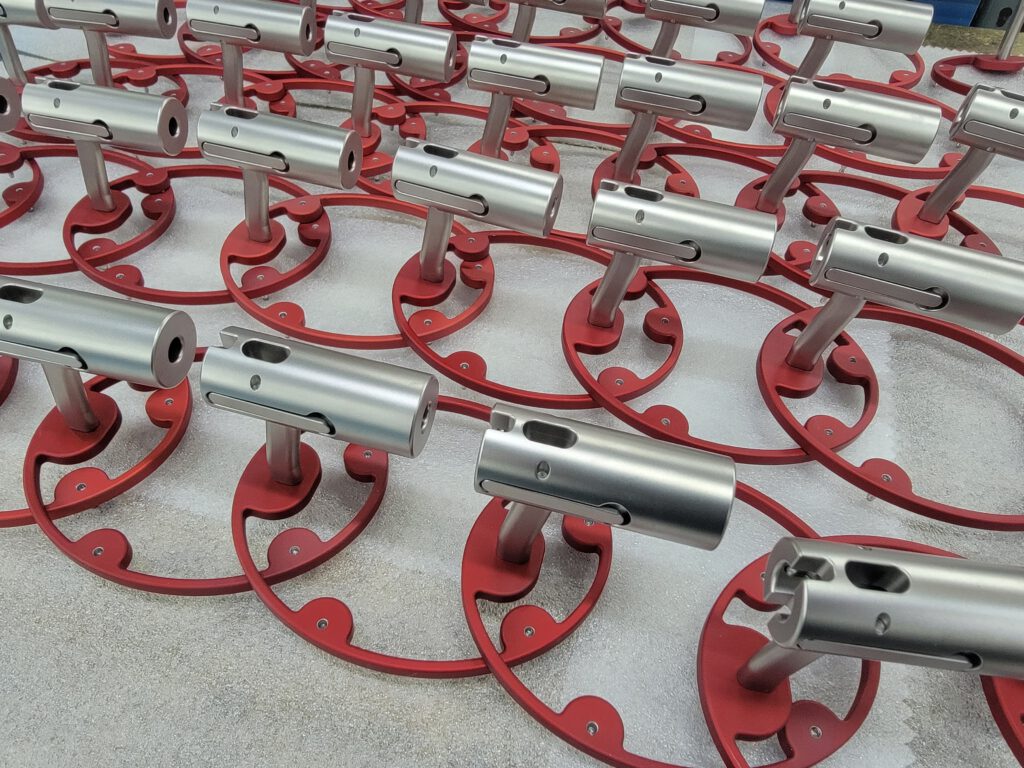
CNC milling is a highly versatile manufacturing process that produces precise and complex parts from various materials. It begins with a computer-aided design (CAD) model or a digital layout that serves as the blueprint for the part to be machined. This design is translated into instructions (G-code) that guide the movements of the milling machine.
In the first step, a solid block of material (workpiece) is secured onto the milling machine’s work table. The machine then uses rotating cutting tools to remove material from the workpiece according to the programmed instructions. They can move along multiple axes simultaneously, allowing for intricate shapes and precise dimensions.
The movements of the cutting tools are precisely controlled by the machine’s computerized system, which receives input from the G-code instructions. This system coordinates cuts’ speed, direction, and depth, ensuring accuracy and consistency throughout the machining process. Additionally, modern CNC machines often feature advanced capabilities to optimize the machining process further.
Chips and debris are generated as the tools remove material from the workpiece. These particles must be effectively managed to maintain the quality of the machining process. Once the machining is complete, the finished part is carefully inspected to ensure it meets the required specifications. Implementing proper post-processing procedures to optimize the part for its intended application is also crucial.
Benefits of Precision Milling
Precision milling offers the following benefits across various aspects of manufacturing:
Precision and Efficiency
Precision milling can achieve exceptionally accurate and consistent results. CNC machines utilize computer-controlled movements to execute precise tool paths, ensuring that each cut is made accurately. This level of precision is crucial for meeting tight tolerances and specifications required in various industries, such as aerospace and medical device manufacturing.
Repeatability
Computer-aided milling machines can reproduce complex machining operations consistently, ensuring that each part is virtually identical to the next. This level of repeatability is essential for maintaining quality standards, especially in industries where consistency is paramount, such as automotive and electronics manufacturing.
Cost-Effectiveness and Reduced Waste
Computer-aided machines optimize tool paths and minimize material removal, resulting in less waste and higher yields from raw materials. This lowers production costs and minimizes ecological impact, making precision milling a sustainable manufacturing solution. In addition, the technique eliminates the need for rework and corrective actions, further driving down costs and improving overall profitability.
Complex Geometries
Precision milling excels at machining intricate shapes and complex geometries that would be challenging or impossible to achieve using traditional methods. CNC machines can also execute all tool paths with precision, allowing for the creation of highly detailed components with tight tolerances.
Versatility
Milling machines can work with various materials — including metals, plastics, and composites — making them suitable for diverse industry applications. They can also accommodate different tooling options and machining strategies. This allows manufacturers to produce parts and components with a wide range of geometries and specifications.
Quick Prototyping
The technique can produce prototypes with high accuracy and consistency, providing valuable insights into product performance and functionality early in development. This accelerated creation cycle reduces time-to-market, enables faster innovation, and facilitates more efficient product refinement. It ultimately gives manufacturers and companies a competitive advantage in dynamic markets.
Scalability
CNC machines can easily adjust production rates and tooling setups to meet changing demand, providing flexibility and agility in production planning. This scalability enables manufacturers to efficiently manage fluctuations in demand and optimize resource utilization, which maximizes productivity and profitability. It also allows manufacturers to explore new business models, such as lean production practices.
Emergence of Robotic Systems for High-Volume Production
The development of robotic systems for high-volume production has revolutionized manufacturing by significantly increasing efficiency and reducing labor costs. Here are some of the most notable systems that have transformed the manufacturing landscape:
Robotic Pallet Exchanging Systems
Tool Changing Automation
Adaptive Machining and Collaborative Robots
IoT Integration for Smart Milling
Robotic pallet exchanging systems in milling operations streamline material handling by automatically loading and unloading pallets onto CNC machines. They use robotic arms to exchange pallets efficiently, minimizing downtime and increasing productivity. Additionally, they contribute to improved workplace safety by reducing the risk of injuries associated with manual material handling tasks.
Robotic loading systems improve manufacturing efficiency by automating material handling processes, reducing manual labor, and minimizing downtime, leading to increased throughput and productivity. They ensure precise handling of workpieces on CNC machines, minimizing errors and enhancing component quality. Additionally, these systems enhance workplace safety by automating heavy workpiece handling, reducing the risk of accidents, and optimize resource utilization by maximizing machine uptime, thereby improving overall production efficiency.
Tool changing is the process of swapping cutting tools on milling machines during machining operations. Automation eliminates the need for manual tool changes, saving time and reducing the risk of errors or accidents. By switching between different tools automatically, CNC machines can execute complex machining tasks without interruption.
Adaptive machining with robotics revolutionizes milling processes by integrating robotic systems with machines to enhance flexibility and efficiency. These systems can dynamically adjust cutting parameters and tool paths based on real-time feedback from sensors, optimizing performance and reducing cycle times. They can also collaborate seamlessly with human operators.
Integrating Internet of Things (IoT) technology into milling processes enables real-time monitoring and optimization of machine performance. Sensors installed on computer-aided milling machines collect data on parameters such as temperature, vibration, and tool wear. This approach allows for predictive maintenance and early detection of potential issues.
Why Work With Us for CNC Milling Projects
At Unity Precision Manufacturing, our commitment to excellence is reflected in our state-of-the-art milling services. These include advanced capabilities such as 4th- and 5th-axis machining. With these cutting-edge technologies, we can achieve complex geometries and intricate designs with unparalleled precision and efficiency.
Furthermore, our milling machines undergo Installation Qualification (IQ) and Operational Qualification (OQ) processes to guarantee performance and reliability. IQ verifies that the machines are installed correctly and according to manufacturer specifications. On the other hand, OQ validates that they operate consistently within defined parameters and meet predetermined performance criteria.
Boost Your Production Efficiency With Unity Precision Manufacturing!
Looking for precision manufacturing expertise that exceeds expectations? Unity Precision Manufacturing is your trusted partner for your machining needs! With our commitment to excellence and state-of-the-art technology, we deliver unparalleled quality and reliability in every project. We also pride ourselves on our dedication to customer satisfaction.
Contact us today to learn more about our services!